What does material innovation look like in architecture today? As architects push for greener, healthier designs, material selection becomes ever more important. Dr. Andrew Dent, executive vice president of research for Material ConneXion, a New York-based consultancy for designers with an in-house materials library, considers a material innovative “if it moves the trajectory of a material’s journey forward in some way.” While he has great hope for bio-based materials in the future, he notes the challenge is that very few natural materials, whether spider silk or algae, last as long as we want them to. “So, for us, innovation is taking existing materials and finding better and more sustainable ways of using them,” Dent said. “There is no such thing as sustainable materials. It all depends on how you use them.”
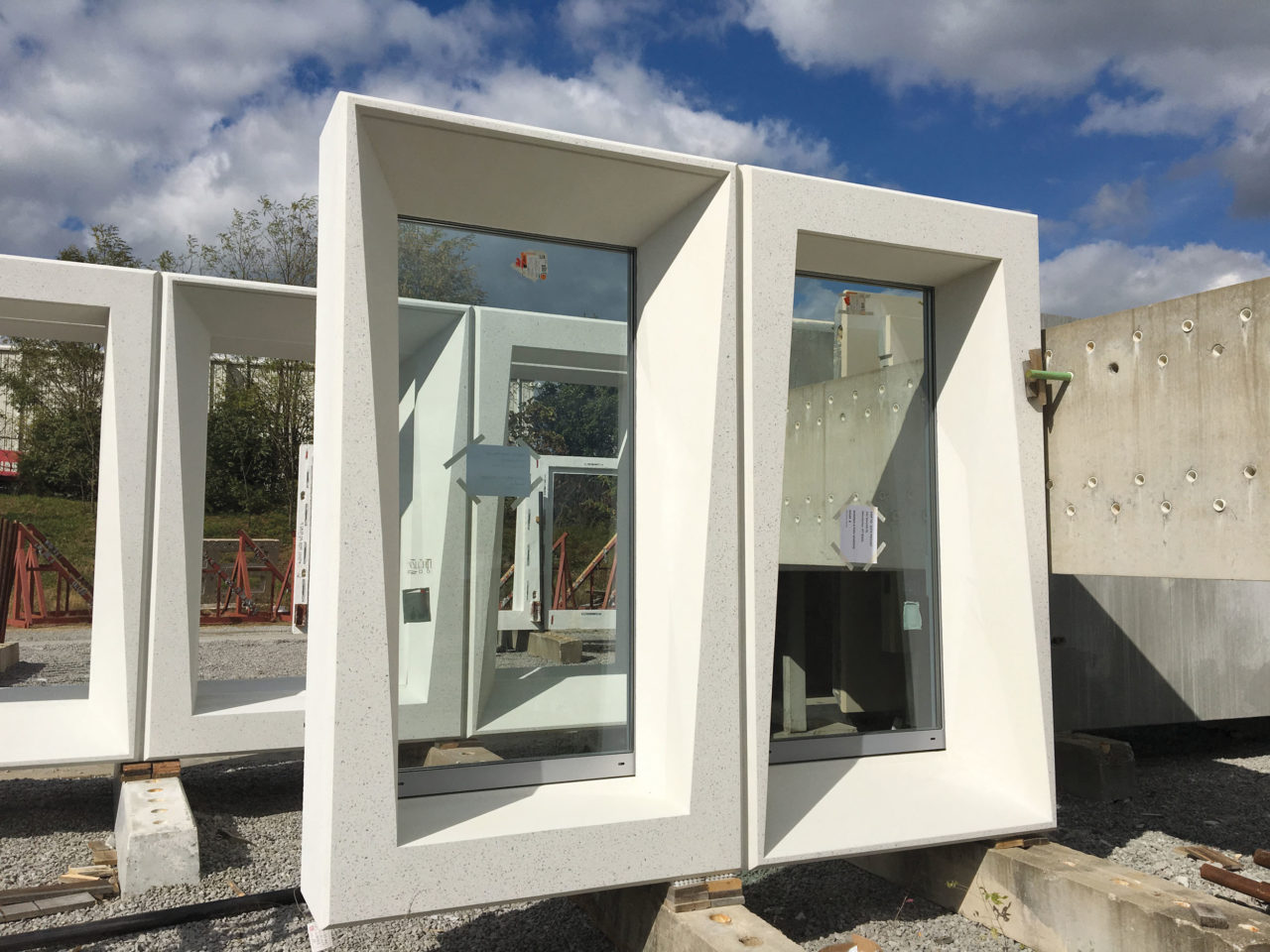
Two projects nearing completion, both firsts of their kind, demonstrate this incremental approach to innovative, sustainable materials in different ways. One South First, a new mixed-use building by COOKFOX under construction along the Williamsburg, Brooklyn, waterfront, embraced futuristic technologies to create its precast concrete façade with large-format 3D printed molds. Harvard HouseZero, a single-family residential retrofit in Cambridge, Massachusetts, went back to basics by sourcing the most natural materials that the architect, Snøhetta, could source locally.
The precast concrete façades of One South First—a 42-story building composed of two interconnected towers, whose shape was determined by SHoP Architects in a 2013 master plan for the Domino Sugar Refinery site—were inspired by the material that used to be produced there: sugar. In crystals or cube form, sugar is geometric, reflective, and textural but sharp. Precast’s material properties suited the concept, explained COOKFOX architects Pam Campbell and Arno Adkins, who were partner-in-charge and co-manager of the project, respectively. Furthermore, they wanted the building skin to “do something performative as opposed to just aesthetic,” said Campbell. “The shaping of the façade, which was more simply possible because of the use of precast, was all about solar strategies.” The windows, whose metal frames are cleverly concealed by the precast, were factory-installed into the panels. The concrete partially shades the windows, contributing some energy savings by taking into account each façade’s solar orientation, but necessitating an extra-deep (20-inch) panel with a lot of variation. COOKFOX brought on Gate Precast, an architectural and structural precast company headquartered in Jacksonville, Florida, early in the project.
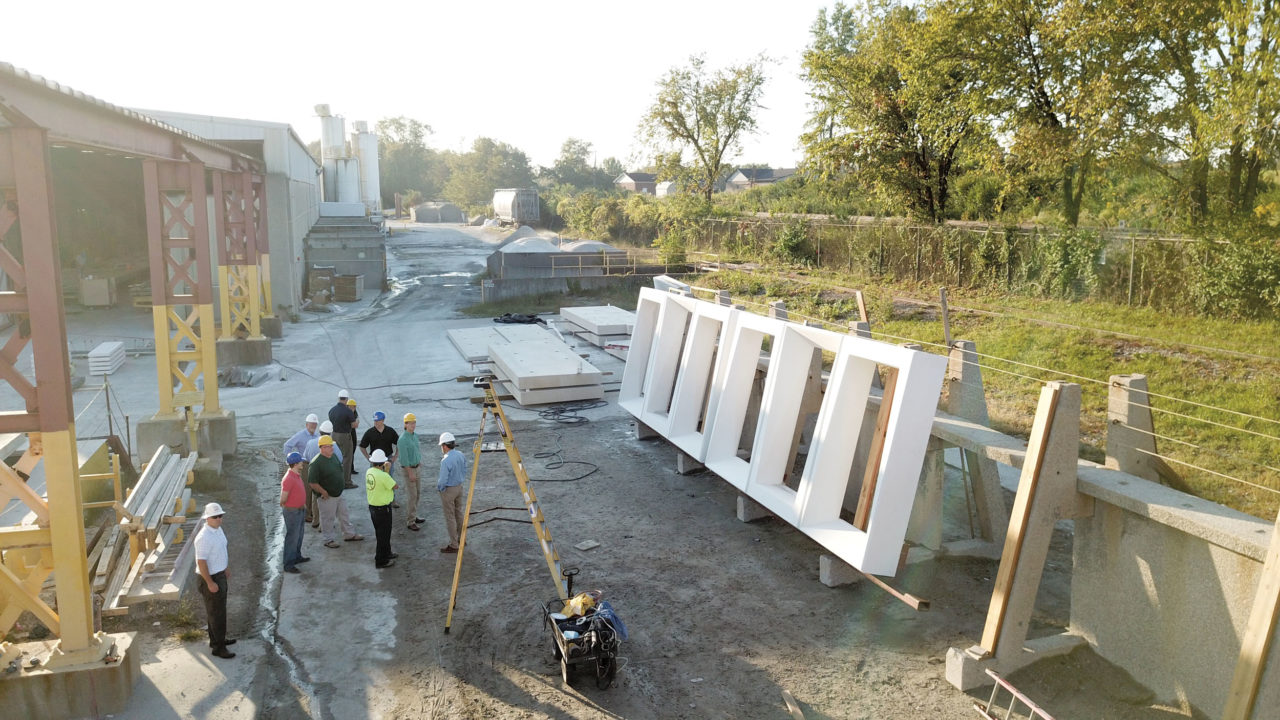
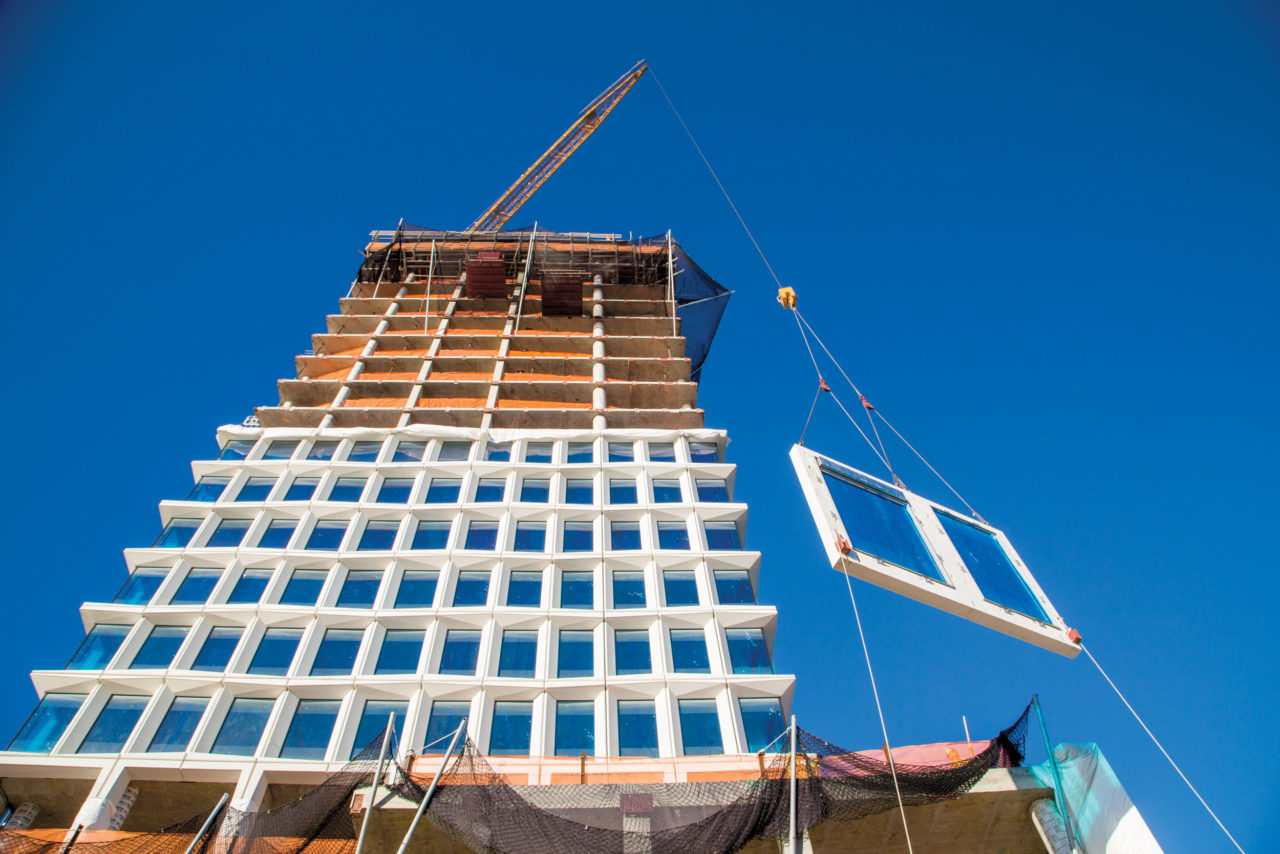
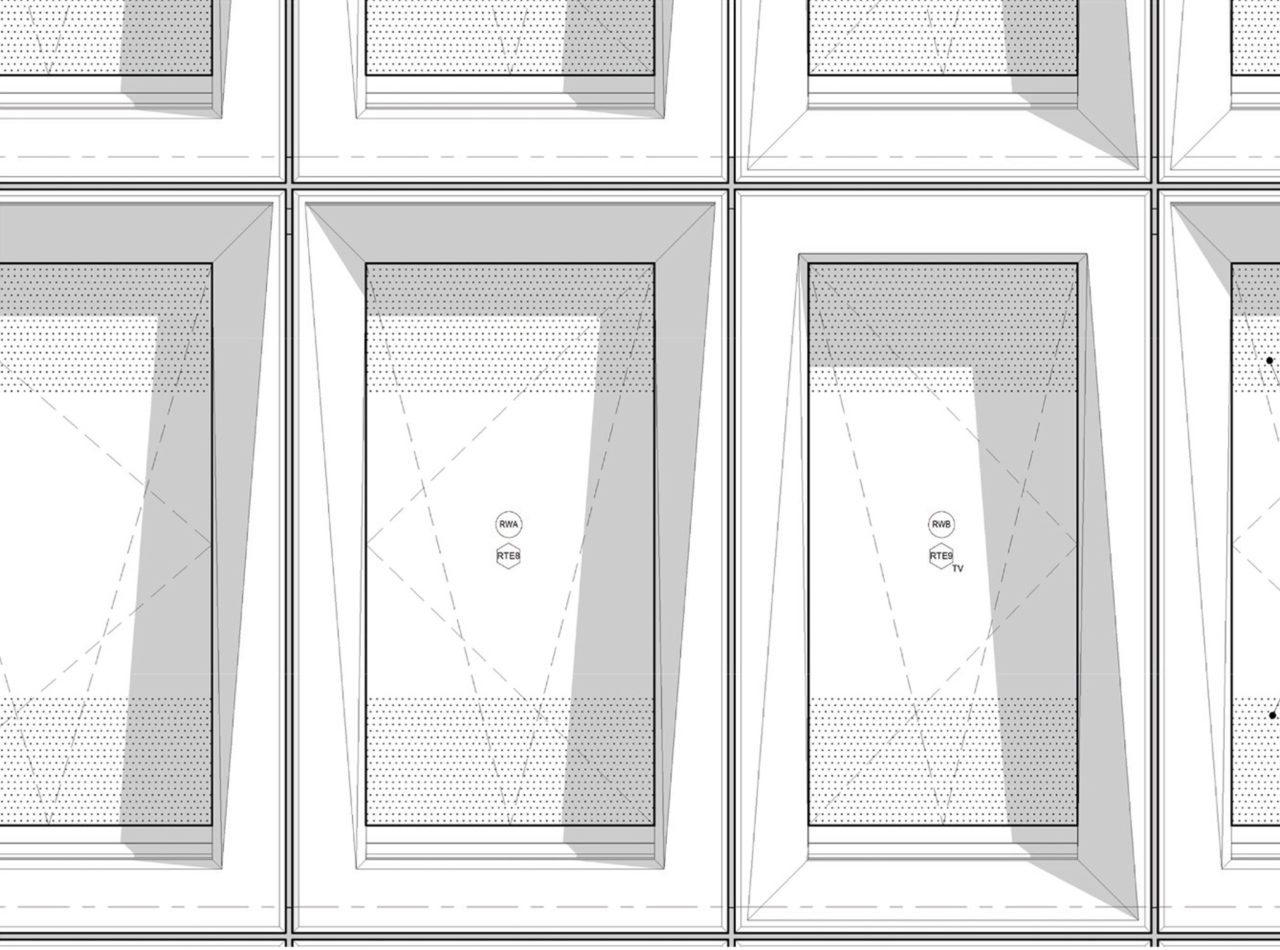
Gate Precast’s senior vice president of engineering, Steve Brock, had already been working with Oak Ridge National Laboratory on 3D printed molds for precast concrete when they became involved on the Domino Sugar project. Traditionally, custom precast molds are made out of wood and assembled by skilled carpenters. With One South First’s very tight schedule, Dean Gwin, president of Gate, noted that the company “simply didn’t have the mold-building craftsman available for that many molds.” So it became the first building to employ this new technology for precast concrete molds.
“It was a research project, because it had never been done on the scale we were trying to do it,” said Brock. He explained there was a lot of trial and error: which plastic to print with (they used an ABS plastic with carbon fiber reinforcement); how much material to use in the print (not overprinting or underprinting); and whether the concrete in the molds would vibrate properly (to get air bubbles out). “They just came out requiring less work after the concrete was cast in our yard than the wood ones would,” Brock said. This is partially due to the nature of the 3D printed mold itself.
Fresh out of the 3D printer, a mold has a corduroy texture from the layers of material built up by the printing process. Then it gets sanded down by a CNC machine. The result is a much smoother and sharper panel than one can achieve with wood molds, which require coatings and caulking over joints and seams to make them watertight for pouring. This perfectly suited the crystalline geometry that was desired for One South First. The architects decided to polish the flat front faces of the panel, highlighting the concrete aggregate—a very bright white sand with mica particles—while the angled faces, which slope away from the glass, were treated with an acid wash. “It’s got that slightly sugary feel to it—not super smooth, but not heavily textured,” said Campbell. “You get these really crisp edges, which highlighted the design idea in the first place: this play of light and reflection, shadow and shade.” Over 100 different panel types were produced.
The 3D printing process allowed for the variation needed for the solar shading at a speed, cost, and aesthetic that fit the needs of the project. But ABS plastic with carbon fiber is not the most environmentally friendly material, although experiments by the University of Tennessee are working to re-pelletize the material to be printed with again. What most excites Brock of Gate Precast is their work with Oak Ridge on a bio-mold composed of polylactic acid, which is derived from plant starch, and wood flour, a byproduct of the furniture industry in the area. Additionally, combining 3D printed molds with ultra-high-strength concrete or lightweight concrete, which both have sustainable benefits, when printing costs come down.
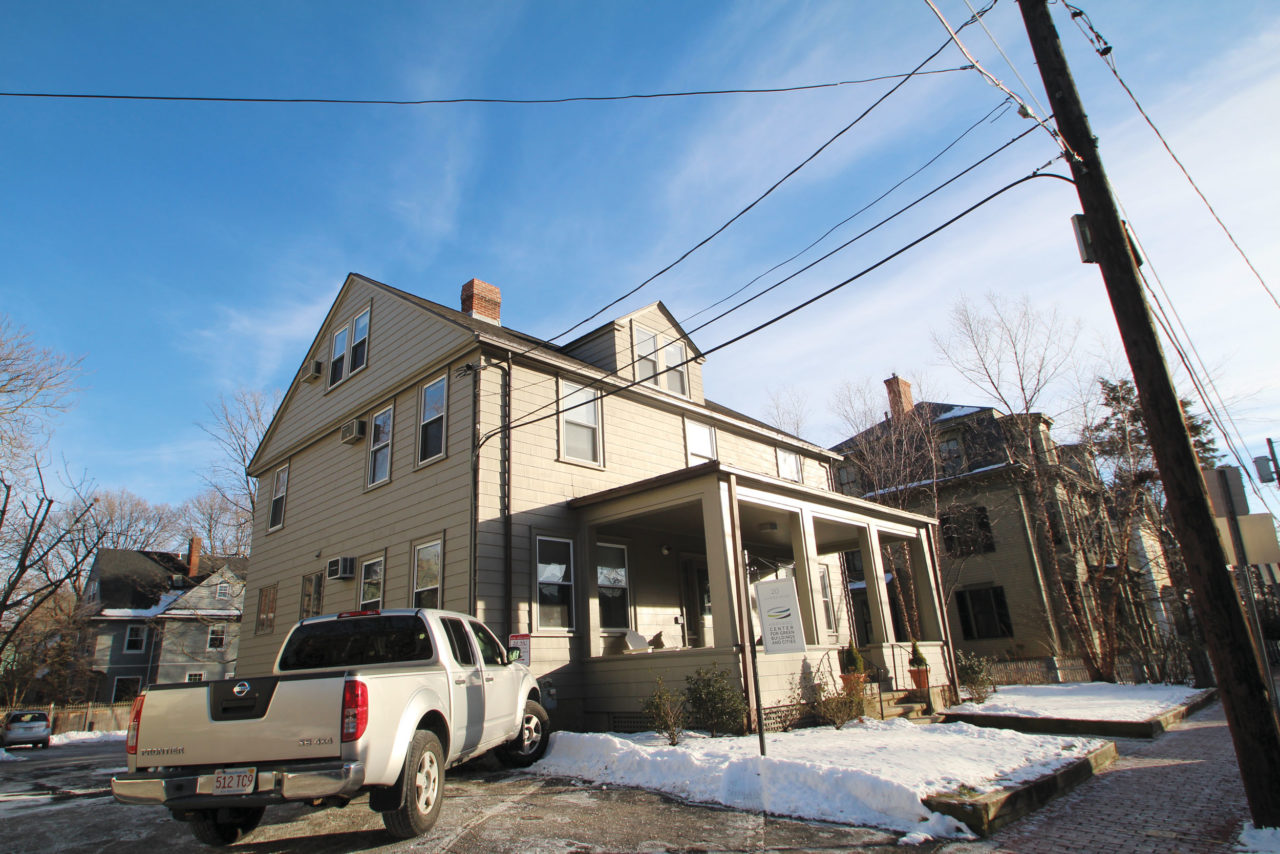
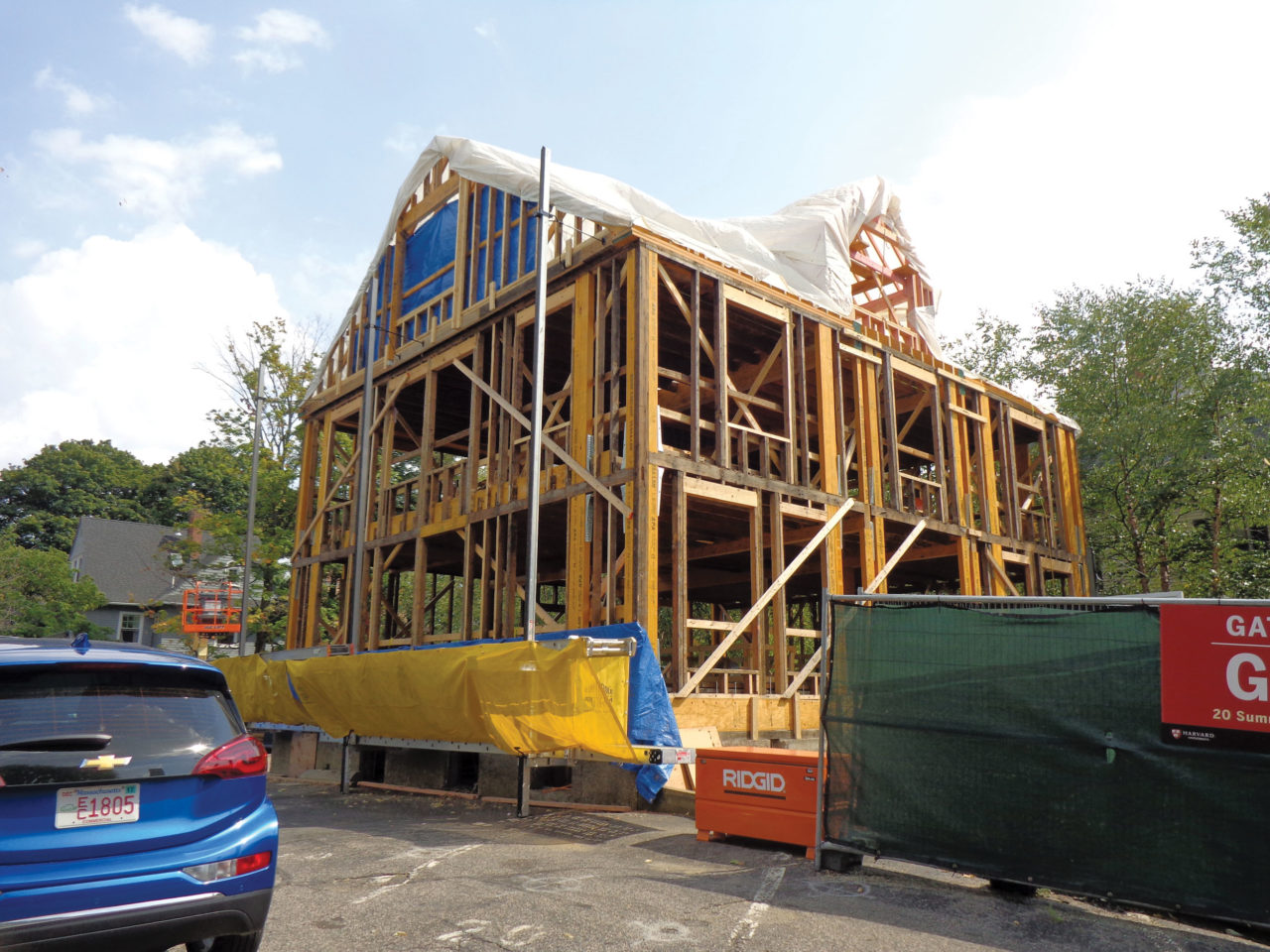
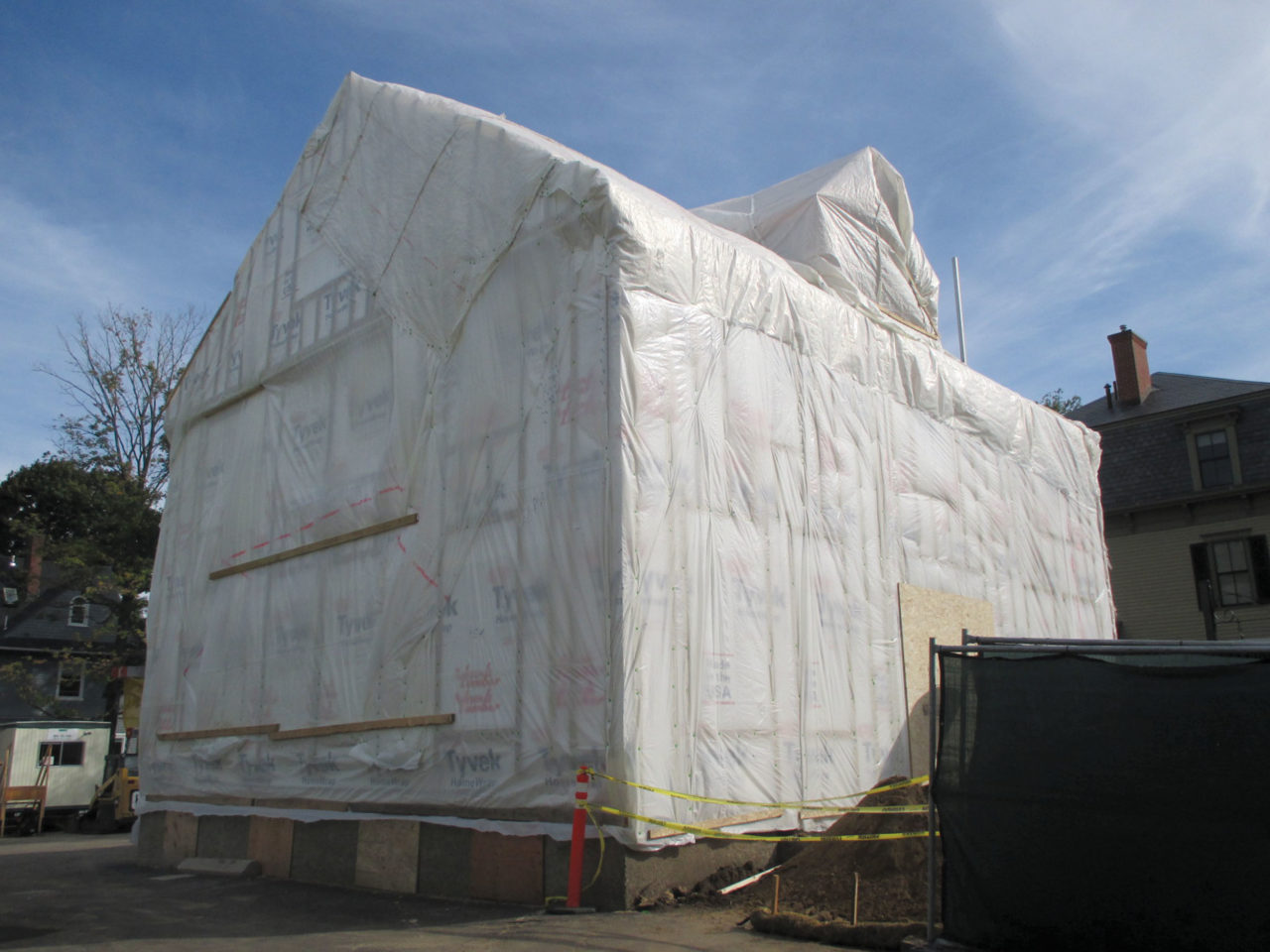
In Cambridge, Harvard’s Center for Green Buildings and Cities (CGBC) and Snøhetta converted a single-family house near the university’s campus into a living laboratory and prototype—which has never been done before—in the hope of demonstrating and learning how we can retrofit existing housing stock to be radically more efficient. The house requires almost zero energy to operate and has zero carbon emissions, including embodied carbon within materials.
If One South First’s material approach was high-tech, Harvard HouseZero’s approach was low-tech. Architect Aaron Dorf, the director of the project, explained that the firm achieved these ambitious goals in part through very careful material selection. “We really need to find ways to radically or incrementally reduce the emissions of building practice,” he said. “The most direct way to do that is to seek out the most natural and nearest source of materials that also require the most minimal amount of processing.” Accordingly, the house employed a variety of locally-sourced, natural materials, such as white cedar shingles, birch plywood, and recycled brick. Dorf cited both the Living Building Challenge and Harvard’s Office for Sustainability for having helpful lists of materials and chemicals to cross-reference selections against.
The white cedar shingles, for example, illustrate the decision-making process behind the project’s material choices. The house is in a historic district, so the exterior cladding needed to fit in aesthetically in order to get construction approval. White cedar is local to the region, and the architects left the shingles untreated since cedar has a natural oil in it, so it does not require a finish. This means less maintenance and therefore less chemical use, over time. To clean the shingles, all that is needed is water and vinegar.
One product that was particularly challenging to source was insulation. Dorf noted that “insulation is one of the highest carbon materials that goes into the house. So reducing the carbon there, without affecting the performance, was really critical.” They wanted a non-petroleum based insulation, but the types of products they were looking at aren’t as prevalent in the U.S. market as they are in Europe or Canada. “There are things that get eliminated because they can’t be sourced or sourced fast enough,” he said.
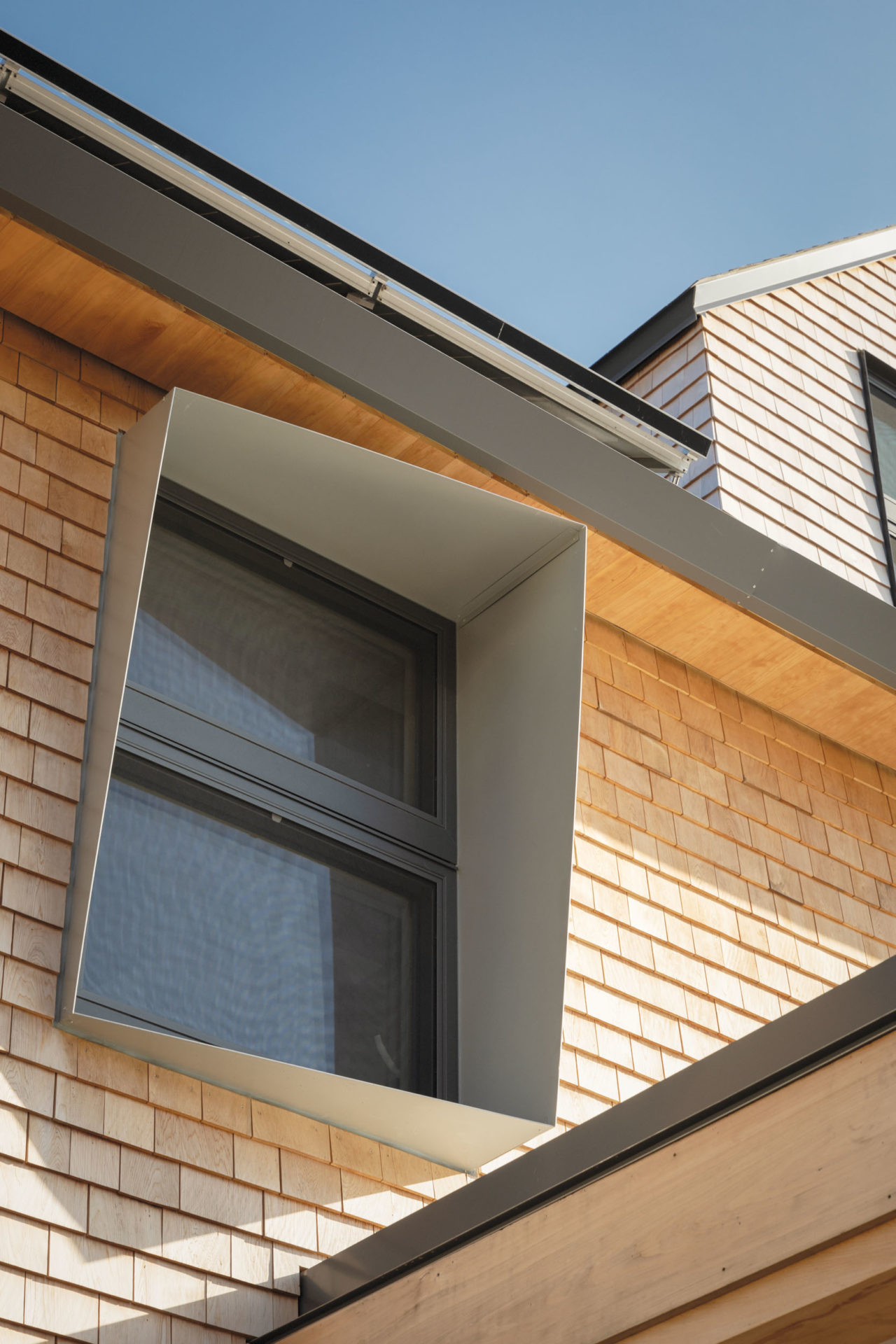
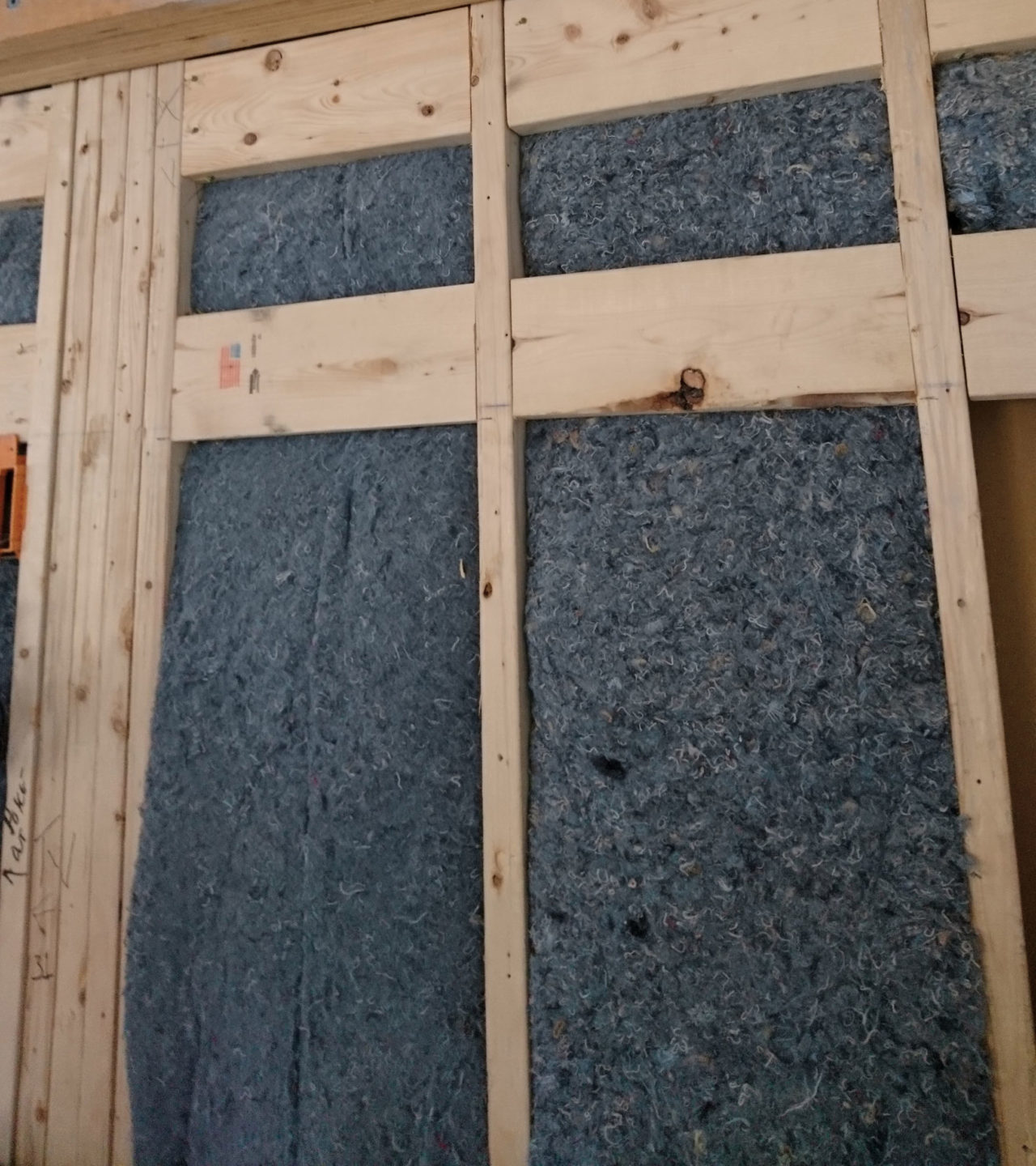
The team eventually selected a wood fiberboard insulation for exterior walls above grade and a recycled denim fiber insulation for interior walls. (The importance of the house’s material selections is such that Harvard does not want to release specific product information until the house has been tested for at least a year). The insulation selected required Snøhetta to entirely rethink the wall cavity construction, ensuring constant ventilation like a rainscreen, as well as the construction process itself. It was its own education, Dorf explained. “We had to basically make them tent the house over during the construction process,” he said, “because you have these water-sensitive things that will be great once they’re fully sheathed. But in the interim, you can’t leave them exposed to the elements. We had to make sure you treat this building differently at every step of the way.”
While the material approach to Harvard HouseZero was rooted in the natural, the project itself employed the latest technologies to the fullest. It has hundreds of temperature, humidity, air speed, air pressure, and occupancy sensors embedded throughout, which creates a real-time computational fluid dynamic model of the structure for the CGBC. “It’s like when you see them make CGI movies: all the key vertices on a body are measured with a node to recreate how the body works with a computational model,” explained Dorf. The house’s systems are reprogrammable so the CGBC can experiment with different algorithms to operate it; Dorf thinks the software and algorithms being developed will be applicable to the building industry in the future.
To be innovative with architectural materials is tough, Dent from Material ConneXion admits, because there are maintenance and even safety concerns with using new products. “The problem with architecture is that you need the new innovation that’s just been found, that’s amazing, to last for the next 70 years—which is really hard to expect for any innovation,” he said. But precisely because of the long life span of buildings, if architects can get it right there’s “an opportunity to create a real change.”
On the surface, neither One South First nor Harvard HouseZero appears radically different from other projects of their kind. But the details tell a different story: incremental improvements in how materials are made and selected reveal the potential for advancing architecture in critical ways.
PROJECT TEAMS
One South First
Architect: COOKFOX Architects, DPC
Richard Cook, FAIA, Partner
Pam Campbell, Partner
Arno Adkins, Senior Associate
Adam Beaulieu, Associate
Avnee Jetley
Seth Brunner
Shira Grossman
Client: Two Trees
Architect of Record: dencityworks architecture
Master Plan: SHoP
Structural: Rosenwasser Grossman, Consulting Engineers
MEP: Dagher Engineering
Civil: Philip Habib and Associates
Geotechnical: GeoDesign Inc.
Exterior Wall Consultant: Vidaris/Laufs Engineering Design
Energy Modeling: YRG/WSP
Acoustic: Longman Lindsay
Landscape: Field Operations
Harvard HouseZero
Lead Architect, Landscape Architect & Interior Designer: Snøhetta
Tine Hegli
Aaron Dorf
Dennis Rijkhoff
Matt McMahon
Anne-Rachel Schiffmann
Karli Molter
Max Obata
Pål Eide Hasselberg
Claire Fellman
Client: Harvard Center for Green Buildings and Cities
Energy/Climate Engineer: Skanska Teknikk (Norway)
Structural Engineering: Silman Associates
MEP/FP Engineering, Lighting: BR+A
Civil Engineering: Bristol Engineering
BAS/Controls/Natural Ventilation System: WindowMaster
Acoustics: Brekke & Strand Akustikk
Code & Accessibility: Jensen Hughes