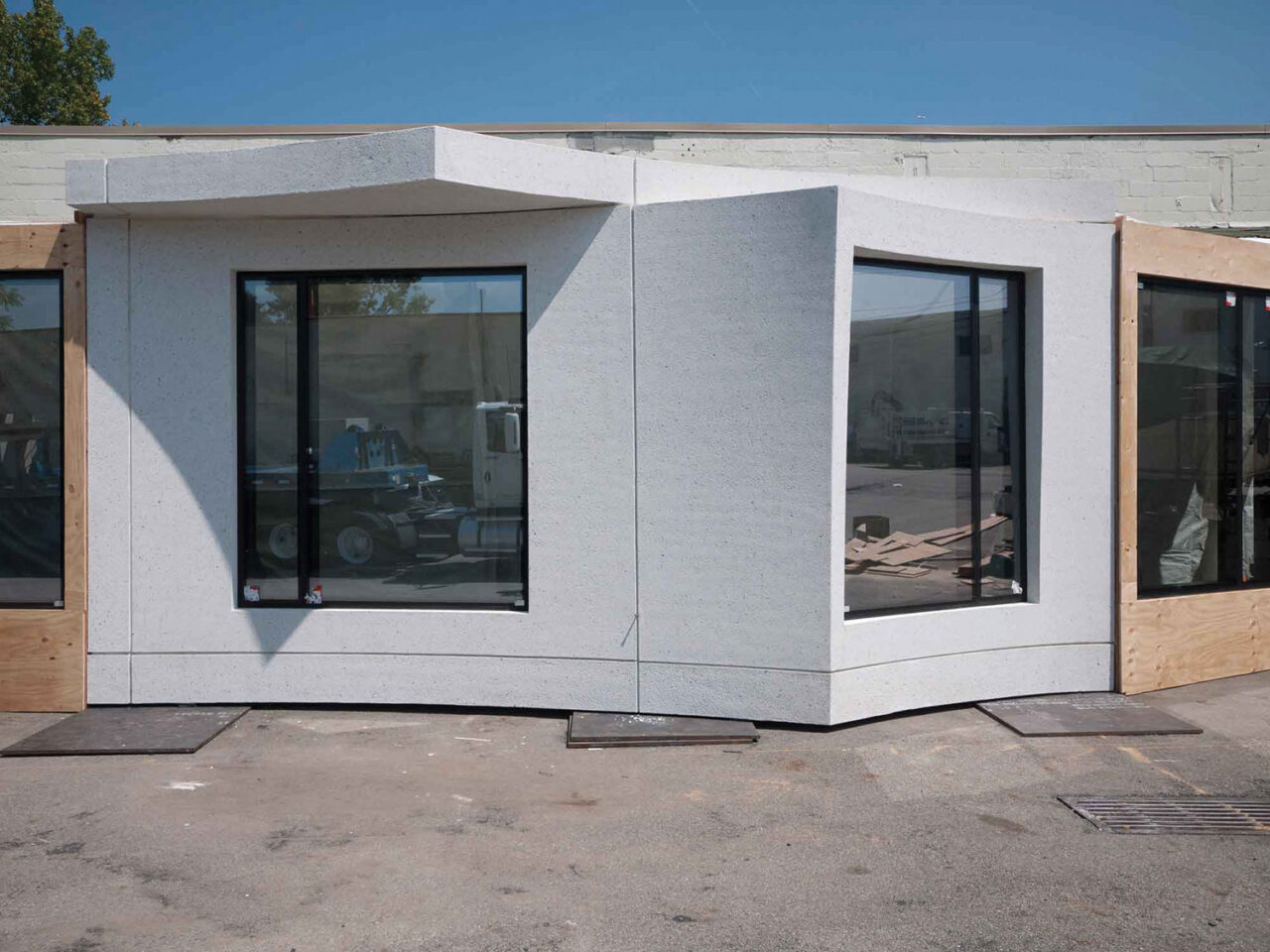
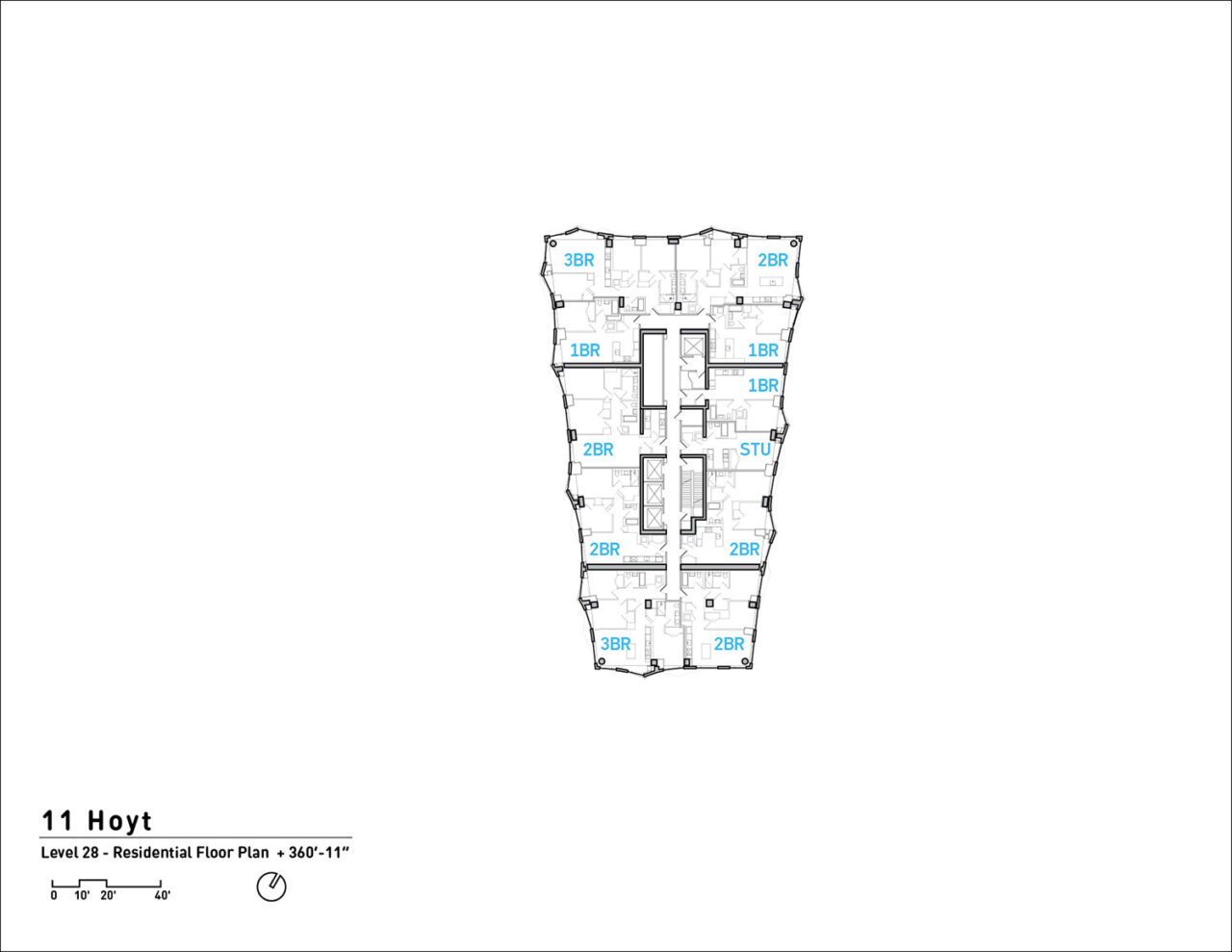
Pre-cast Concrete Façade Panels
11 Hoyt, Brooklyn, NY
Studio Gang
The pre-cast concrete façade panels cladding 11 Hoyt in Brooklyn are designed to take a live load—an industry first for envelopes. Scalloped edges migrate across the high-performance façade of the 57-story condominium tower, push-ing out the plan to maximize views of the neighborhood and create expanded living spaces with built-in window seats as deep as three feet. Prefabrication enabled faster construction, significantly reducing cost and impact to the neighborhood. The 1,155 volumetric wave elements were created by casting the panels onto plywood bent onto CNC-cut ribs. Each panel was formed with more rebar than is typical in flat pre-cast slabs, with reinforcing embedded within for additional stiffness. The design team conducted an in-depth quantities analysis to limit the volume of material used without diminishing the building’s sculptural quality. Exterior projections of up to three feet, nine inches offer the condo building more spatial and visual interest—inside and out—in an efficient way.

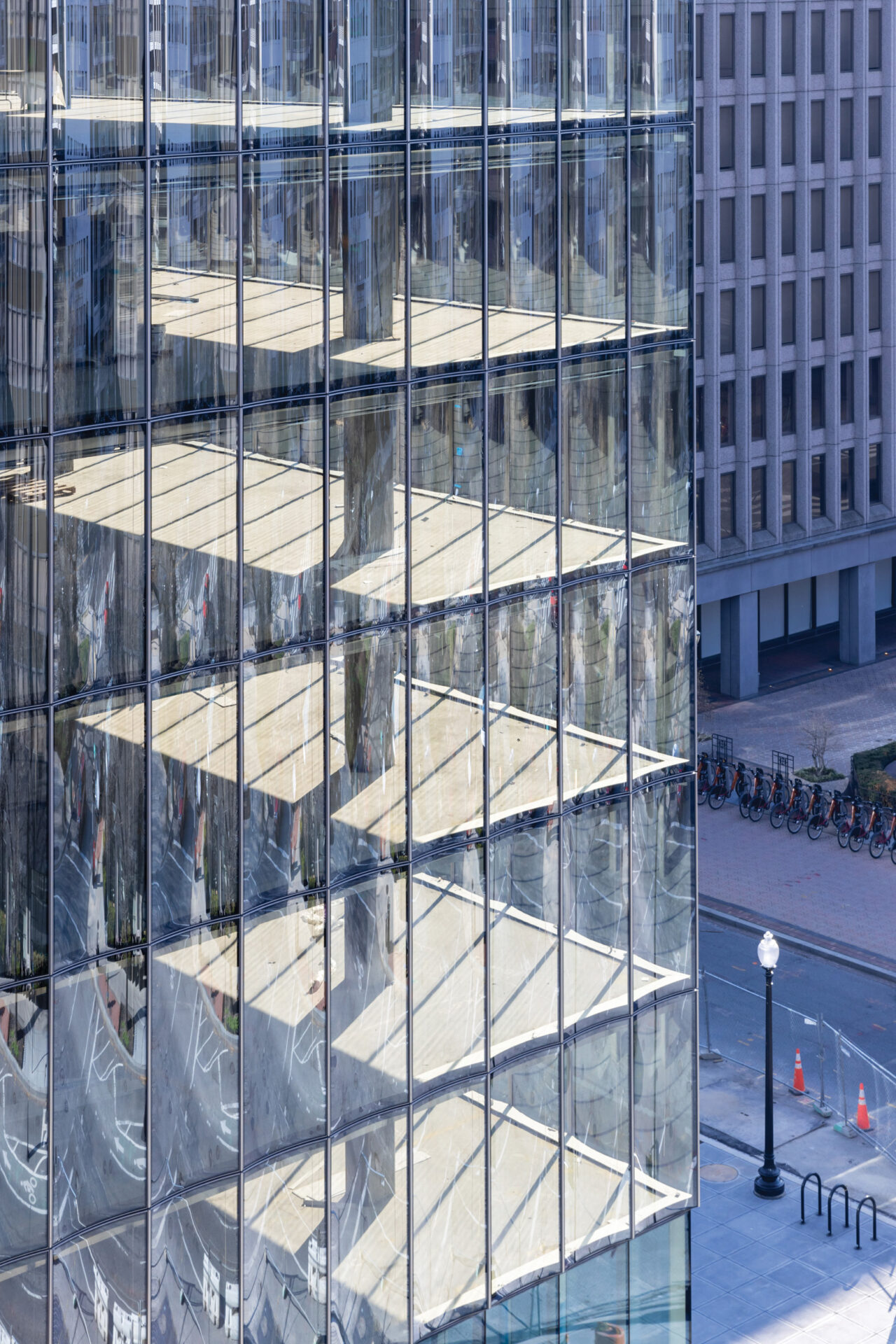
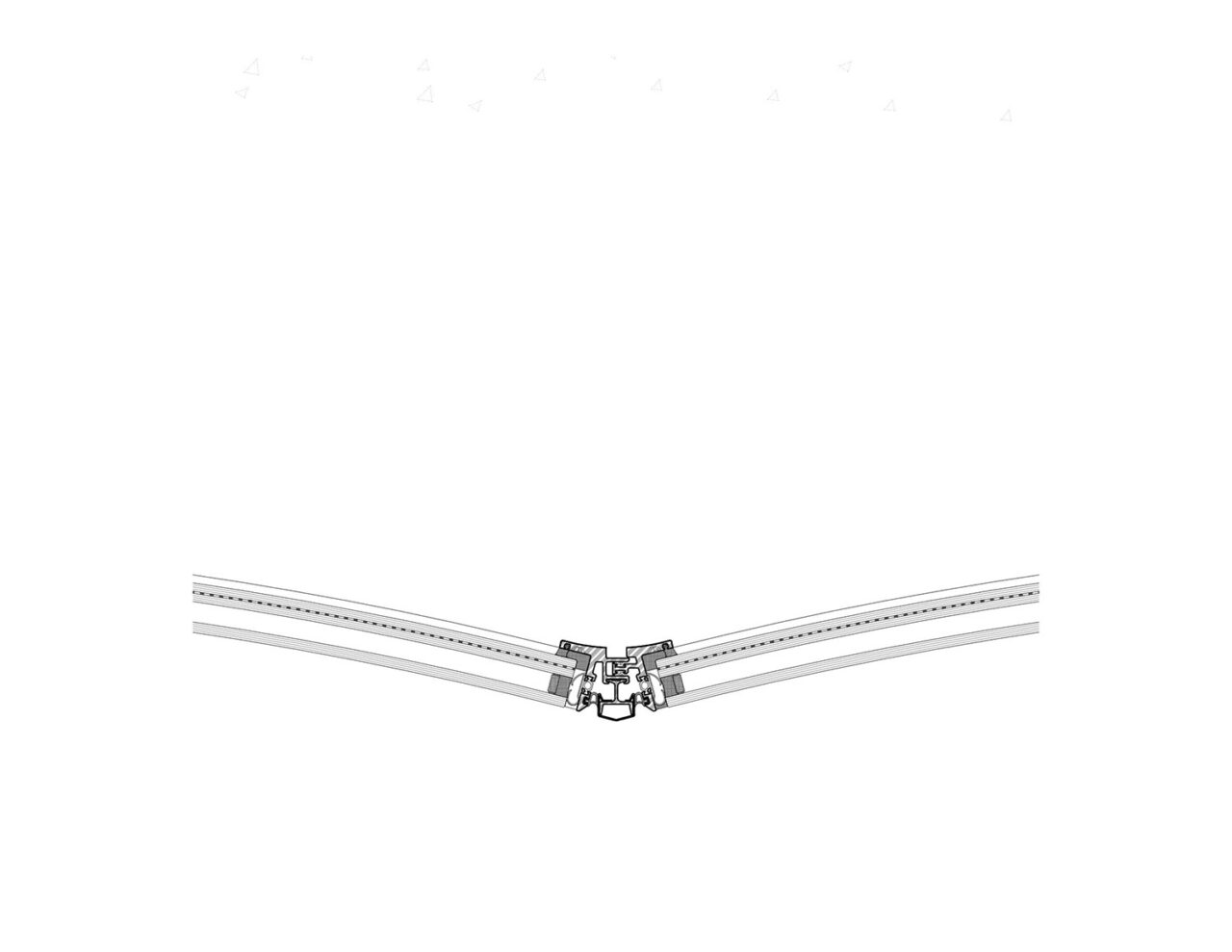
Glass Façade
2050 M Street, Washington, DC
REX
2050 M Street is an 11-story, in Washington, DC, that leveraged its façade to create a memorable identity and provide hyper-transparent, mullion-free, floor-to-ceiling glass for tenants. A total of 978 identical insulated glass panels—measuring 11 feet, three inches tall by five feet wide—were subtly curved to a nine-and-a-half-foot radius using a bending tempering furnace that heats and curves flat glass with geometric precision and no distortion. The inherent rigidity of the curved glass eliminates the need for structural mullions—leaving only a minimalist unitized frame that improves sightlines, increases usable floor area, and reduces the thickness of the monolithic outer lite for greater transparency. A subtly reflective pyrolytic coating on the glass’ exterior and a high-performance low-E coating applied within the glass’ insulating cavity reduce solar heat gain and meet thermal performance requirements. Paired with the fluted panels, this creates an unusual kaleidoscopic effect of repetitive transparency and reflection that simultaneously animates and dematerializes the façade.
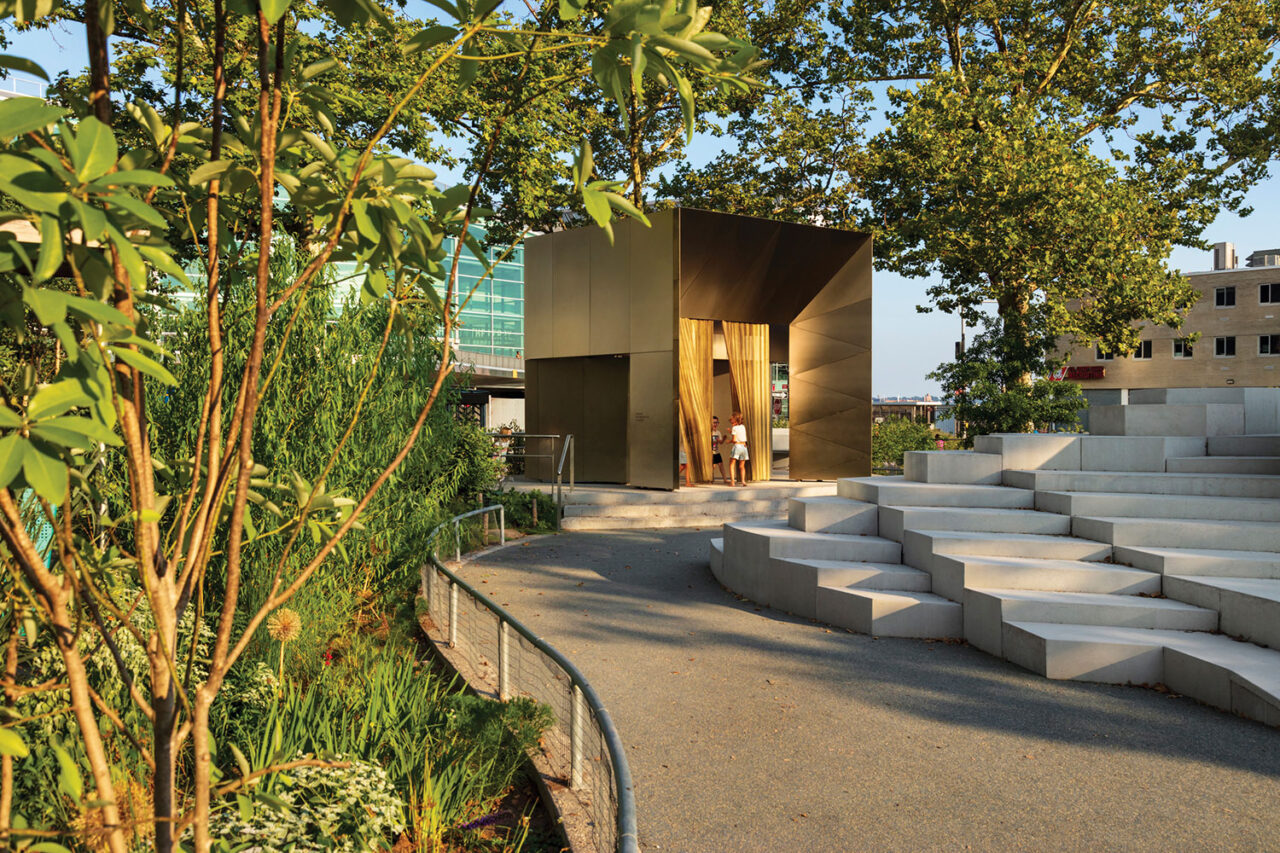
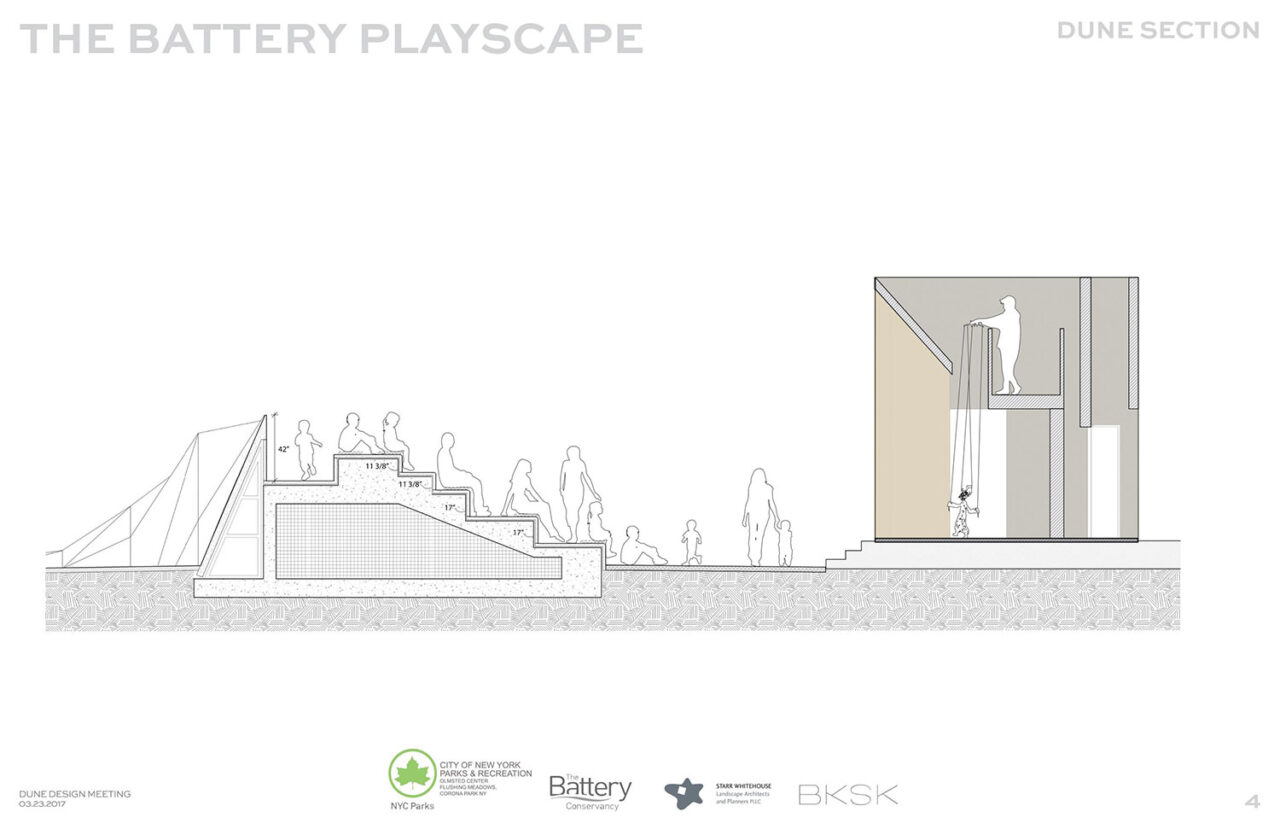
ShowBox Improv Theater
Battery Playscape, Manhattan, NY
BKSK Architects
The Battery Conservancy worked closely with puppeteer Basil Twist and The Jim Henson Foundation to create the ShowBox theater, the first improv theater in a New York City playground. The “jewel” of the Battery Playscape, the 14-foot, two-toned, stainless-steel-clad cube was designed by BKSK Architects and fabricated by SITU Fabrication to withstand water, impact, and contact with lots of little fingers. Used for public performances, local school programs, and imaginative play by the public, ShowBox features a nine-by nine-foot champagne-colored stainless-steel proscenium, completed with a bronze mesh curtain from GKD Metal Fabrics and rigging for student-made scenery. Inside the structure, hooks and rods are available for performers to hang puppets or set pieces when not in use. While the partitions in the theater are all fixed, a concealed door at the back of the theater can be unlocked to allow performers to climb a ladder to the marionette bridge above the stage. A smaller stage for hand puppets is located around the side of the main stage, facing an open area where kids can gather close to enjoy the performance.
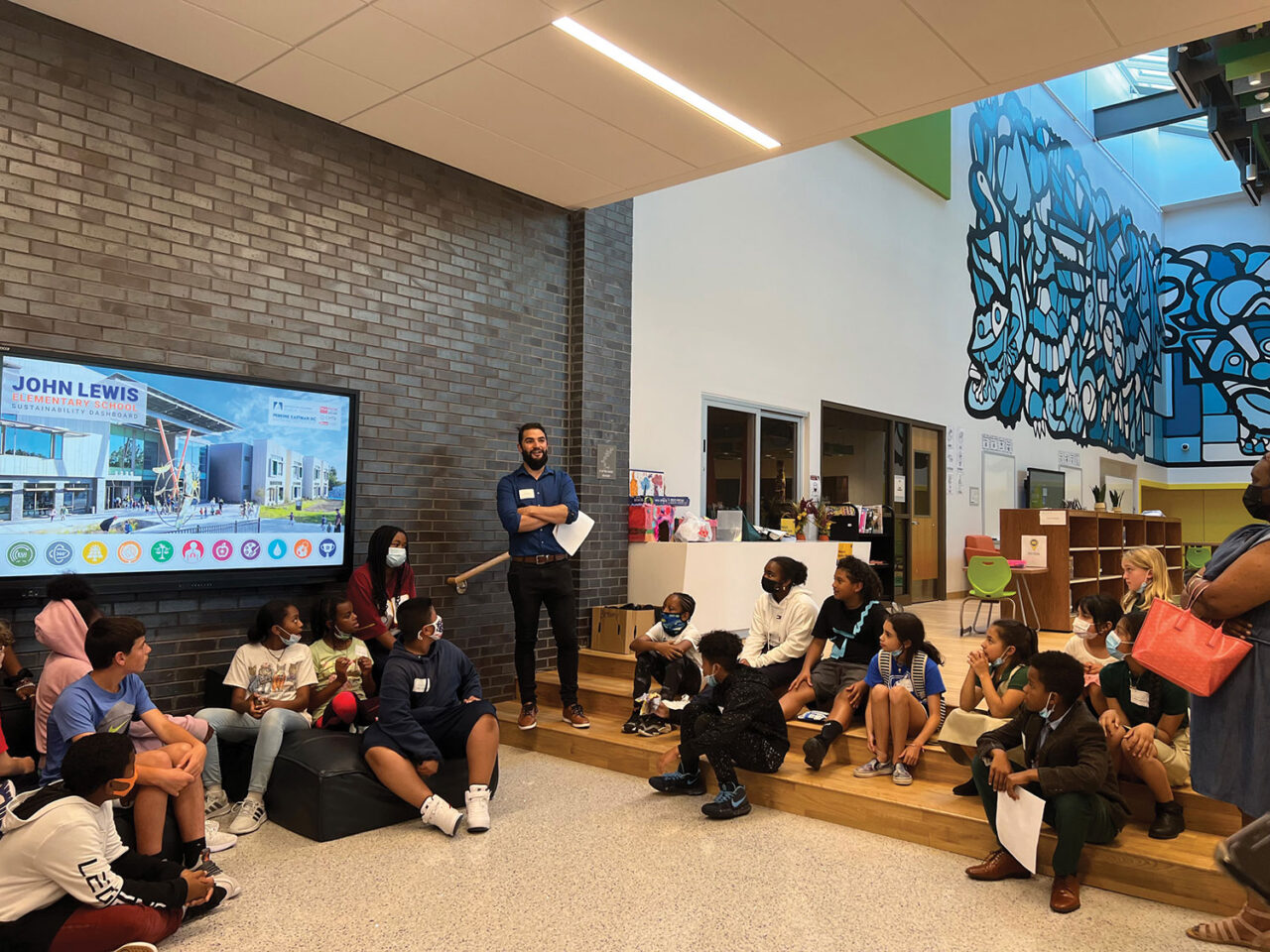
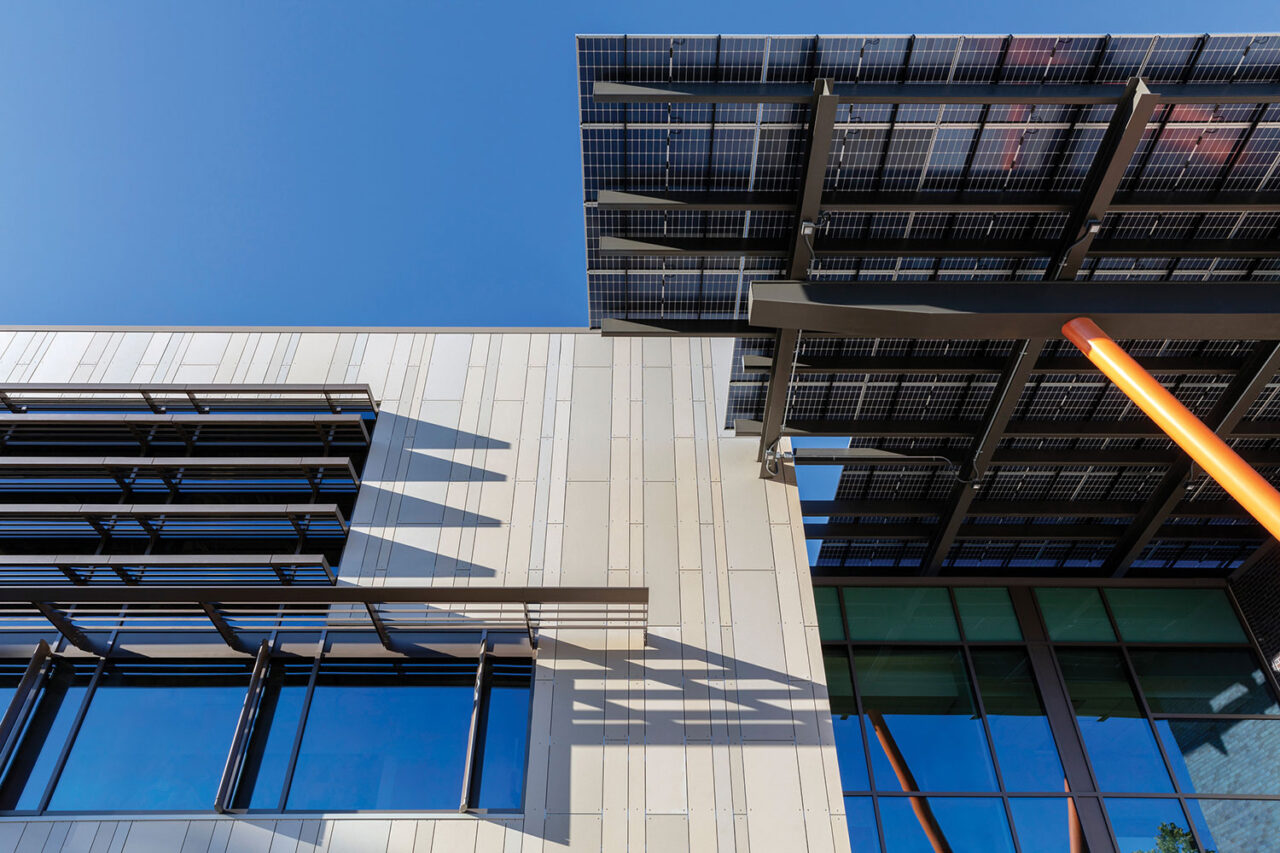
Net Zero Energy Achievement
John Lewis Elementary School, Washington, DC
Perkins Eastman DC
Designed to be the world’ s first Net Zero Energy, LEED Platinum, and WELL-certified school, John Lewis Elementary sets a global benchmark for learning environments. Intended to offer a “Net Positive Education,” the school supports the health and education of students from a daylight, thermal comfort, acoustic, and air-quality perspective. To help accomplish this, pipes from a geothermal well field located beneath the playground and playing field heat and cool air and water, while an air-handling unit provides 30% more outside air than code minimum requirements. Energy use is offset in surplus by photovoltaic panel arrays on the roof used to heat water, satisfy plug loads, and address the electrical needs of the building. Sunshades and light shelves reduce glare and distribute light evenly, while carbon dioxide sensors communicate with building systems to adjust to occupant loads. Finally, on-site bioretention ponds manage and clean stormwater through layers of filtration.
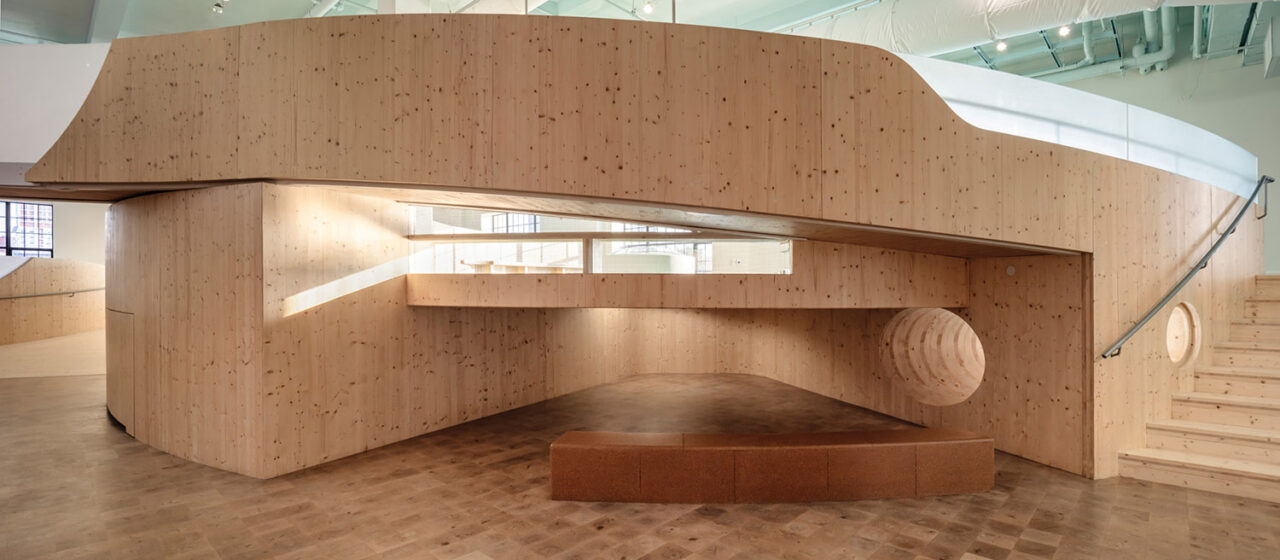
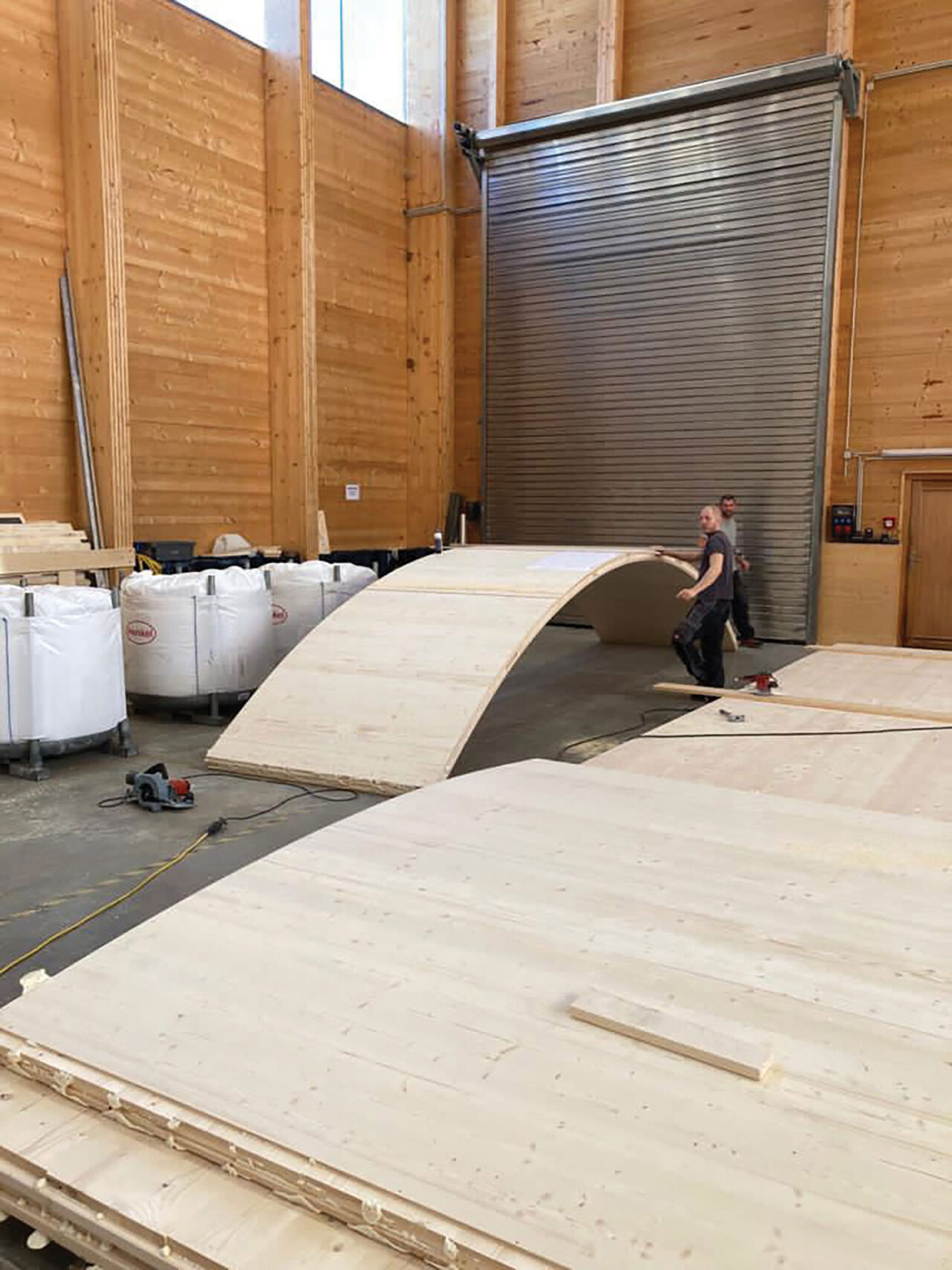
CLT Digital Fabrication
Bronx Children’s Museum, Bronx, NY
O’Neill McVoy Architects
As the borough’s first cultural facility for young children, the Bronx Children’s Museum utilizes natural materials, curvilinear geometry, and spatial flow to connect kids to the Bronx’s natural landscape and waterfront. Walls, guardrails, doors, stairs, and floors made of CLT fabricated with advanced digital technology allow for varying radii arcs to form organic spatial curves—the first use of curved CLT in the U.S. O’Neill McVoy Architects worked with Austrian fabricator KLH to devise a way to make large panels using custom molds with the CLT material, not unlike how Charles and Ray Eames made their breakthrough laminated plywood leg splints in 1943. The CLT panels were site-routed to structurally interlock with recycled acrylic partitions, and clear sealers elimi-nated the need for metal stud assemblies and finishes.
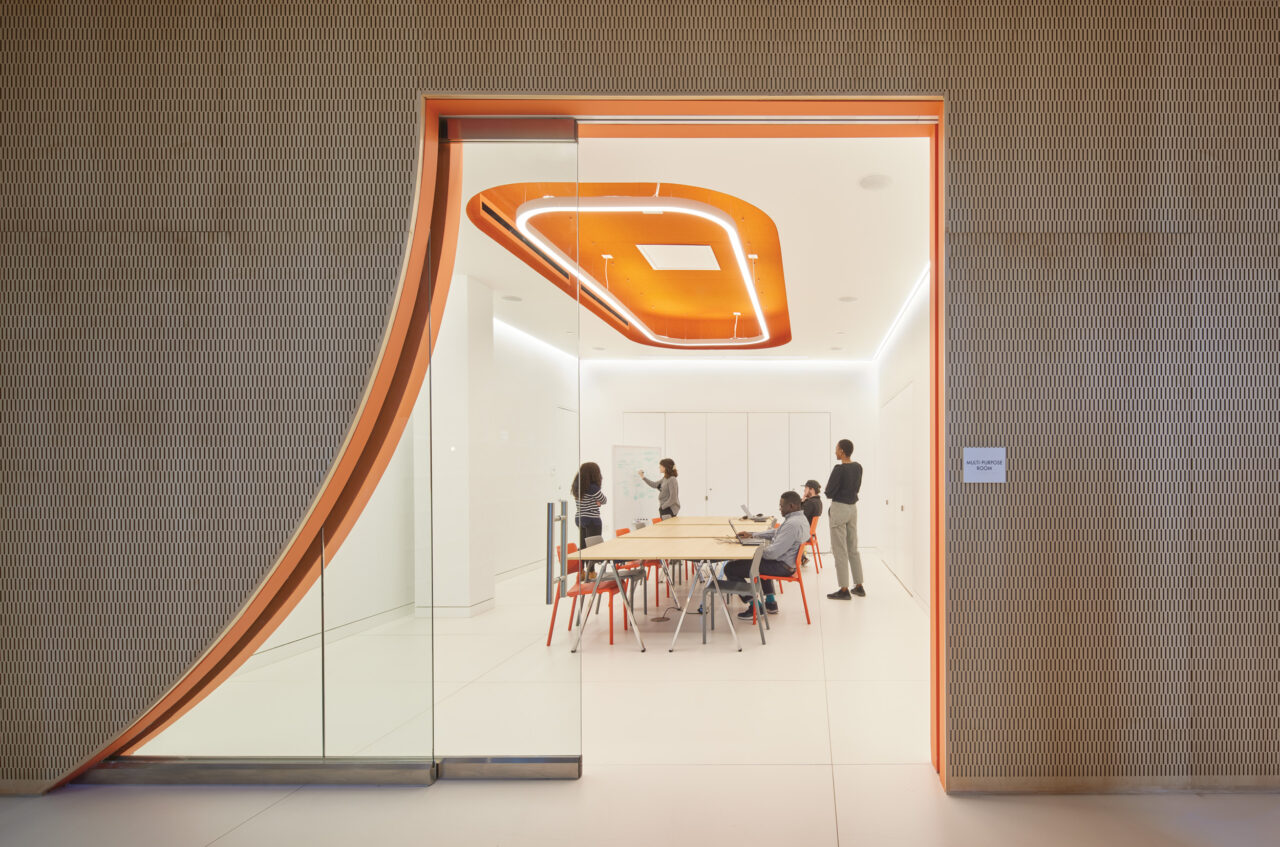
CNC-milled MDF Wall
Adams Street Library, Brooklyn, NY
WORKac
A maple-veneered, CNC-milled, MDF wall surfacing is one of the contemporary interventions integrated into the historic building that houses the Adams Street Library in Brooklyn. Surrounding the children’s section and multipurpose room, the wall’s brick-like pattern adds warmth, breaks up sound in the main reading room, and resonates with the highly textured existing walls and ceilings in the space. At the millworker’s suggestion, WORKac used MDF instead of plywood to create cleaner holes for the pattern. The wall is separated from the ceiling to differentiate between old and new, hide the mechanical equipment, and expose more of the existing ceiling. A curtain-shaped entryway to the kid’s room creates a sense of fun and drama, while a big elliptical opening serves as a “balcony” to allow kids to look out over the reading room to the windows. The community room has the only opening in the pavilion that was required to be closed off acoustically from the rest of the space. To make sure visitors do not walk into the sliding door’s glass, the team created a frit pattern on the glass, mimicking the pattern of the millwork panels.